Новий журнал «Пиво. Технології та Інновації» можна завантажити безкоштовно
ПРОИЗВОДСТВО НАПИТКОВ. Фильтрация в производстве напитковС.К. Данильченко, Генеральный директор ООО «Интер Технолоджи Компании»
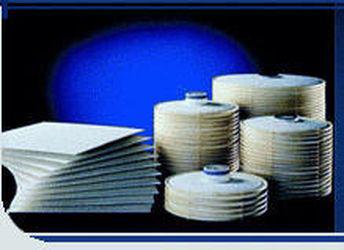
Процессы фильтрации являются одними из основных в производстве напитков, причем с ростом требований к качеству продукции значимость фильтрации возрастает. В современных пищевых производствах фильтрация используется для очистки продукта или сред, контактирующих
с продуктом (вода, газы, пар). Конечной целью фильтрации продукта может быть прозрачность или стерильность, в зависимости от типа продукта и его маркетинговой позиции. Наиболее широко для удаления массовых загрязнений применяется фильтрация через глубинный фильтрующий слой. Сюда можно отнести кизельгуровую и песочную фильтрацию. Песочная фил ьтрация
используется в системах очистки воды и позволяет удалять ил, глину, нерастворимые окислы железа и марганца, сфлокулированные загрязнения и пр. Приобретая песочный фильтр, необходимо учитывать, что размер вышеперечисленных загрязнений зачастую намного меньше, чем размер частиц фильтрующего песка и поэтому эффективность очистки воды в значительной
степени зависит от конструкции фильтра, а именно от организации гидродинамики процесса фильтрации. Очень важно, например, равномерное распределение потока фильтруемой воды по поперечному сечению фильтра, предотвращение образования свищей и застойных зон.
Многие производственники наверняка наблюдали свищи в фильтрационном слое и, соответственно, сталкивались с низким качеством фильтрации, уносом песка при росте перепада давления на фильтре, проблемами со стерилизацией фильтра. Все это последствия неквалифи-
цированного конструирования фильтра. Основным преимуществом песочных фильтров является дешевизна фильтрующего материала и легкость его регенерации, возможность жестких режимов химической или термической стерилизации, а недостатком является потеря устойчивости слоя при росте перепада давления и гидроударах. При помощи песочных фильтров можно достигать требуемой для бутылированной воды прозрачности < 0,1 NTU.
Кизельгуровая фиьтрация используется в основном для удаления сжимаемых органических осадков (дрожжи, бактерии, белковые осадки, мезга и пр.) из продуктов брожения: пива, вина, кваса, сидра, хотя впервые была применена в Германии для очистки питьевой воды. Для
удаления загрязнений из частиц кизельгура создается глубинный фильтрующий слой. В зависимости от характера и количества оседаемых на поверхности слоя загрязнений, в поток нефильтрованного продукта подают новые порции кизельгура. Таким образом, осаждаемые загрязнения и свежий кизельгур наращивают фильтрационный слой. К концу процесса
фильтрации растет глубина слоя и качество фильтрации. При выборе кизельгурового фильтра
рассчитывают поверхность фильтрации и объем осадочного пространства. Важно учитывать максимальное рабочее давление в фильтре. Поверхность фильтра рассчитывают исходя из рекомендуемой удельной скорости фильтрации для данного вида продукта и типа фильтра в л/м2
х час с одной стороны и требуемой часовой производительности фильтра л/час. Часовая производительность рассчитывается из средненедельного объема потребности фильтрата с учетом длительности циклов подготовки и длительности цикла фильтрации, которая в свою очередь может быть ограничена недостаточным объемом осадочного пространства и низким рабочим давлением. Так, например, для цикла фильтрации длительностью 17 часов при росте
перепада давления 0,3 бар/час потребуется ресурс рабочего давления в 5 бар. Понятно, что если равновесное давление насыщения продукта углекислотой высокое, как, например, в случае с игристым вином, то для фильтра с рабочим давлением 9 бар ресурс рабочего давления может составить всего 1,5-2,0 бар. Фильтры с таким высоким рабочим давлением изготавливают лишь
несколько производителей.У нас, к сожалению, практически не применяется кизельгуровая фильтрация для очистки сахарных сиропов. Для оценки качества кизельгуровой фильтрации применяются разные подходы и методики. В пивоварении определяют количество дрожжевых клеток на 100 мл фильтрата (норма до 5 культурных клеток), а также интенсивность рассеяния света в единицах EBC под углами 90º и 25º, в виноделии в единицах мутности NTU (нормально < 1) и также количество дрожжей и бактерий на 100 мл фильтрата (около 0), при фильтрации сиропов контролируют цветность в единицах ICUMSA (норма < 35). Основным преимуществом кизельгуровой фильтрации является ее гибкость, позволяющая перестроить процесс в пределах одного цикла фильтрации. К недостаткам можно отнести нестабильность фильтрационного слоя при росте перепада давления и гидроударах, зависимость от качества кизельгура и проблемы с утилизацией осадка. Для устранения повторного загрязнения отфильтрованного напитка от
прорыва фильтрационного слоя служат трап-фильтры. Для трап-фильтрации в основном используются мешочные и картриджные полипропиленовые фильтры с рейтингом фильтрации 5, 10 или 20 мкм. Картриджные фильтры намного надежнее мешочных и при квалифицированном обслуживании хорошо моются, стерилизуются и поэтому служат долго. Таким образом, глубинная фильтрация в сочетании с трап-фильтрацией обеспечивает удаление из напитков массовых загрязнений с достижением требуемой прозрачности. Современной альтернативой указан-
ным методам является тангенциальная фил ьтрация . Идея этого метода заключается в создании условий, позволяющих фильтрационной среде самоочищаться в ходе фильтрации. Такой эффект
достигается за счет смыва осадка постоянно циркулирующим вдоль фильтрационной поверхности потоком нефильтрата. Рейтинг фильтрации 0,2-0,1 мкм и ниже позволяет получить требуемое для напитков качество фильтрации. Фильтрационными средами в тангенциальных фильтрах являются мембраны, изготовленные из полимера или керамики. Коммерчески наиболее эффективными являются половолоконные мембранные фильтры. Химическая технология производит половолоконные мембраны, обеспечивающие высокое качество фильтрации, высокую удельную поверхность фильтрации, высокую термическую и химическую устойчивость. Наибольшего успеха тангенциальная фильтрация достигла в фильтрации тихих вин. Начав применяться 15-20 лет назад, она уже не оставляет никаких шансов кизельгуровой и картонной фильтрации. Секрет успеха прост – высокая фильтруемость вина, обусловленная выдержкой, и низкая вязкость благодаря спирту. Распространение данного метода в шампанском производстве на несколько лет задержалось в связи с необходимостью создания изобарических конструкций с высоким
рабочим давлением. На рынке производства воды и напитков успешными оказались системы только тех производителей, которым удается очищать мембраны от нерастворимых частиц ила, песка, угля и пр. и санировать их. Такие системы обеспечивают высокое микробиологическое качество и прозрачность уже в течение 5-7 лет и более без замены мембран. Чрезвычайно важной для тангенциальной фильтрации отраслью является пивоварение. Здесь уже давно с началом роста цен на кизельгур и проблем с его утилизацией сформировалось ожидание альтернативы кизельгуровым фильтрам. Низкая фильтруемость пива и необходимость частых характерных для пивоварения CIPов потребовали времени и новых материалов для создания надежных фильтрационных систем. К настоящему времени в мире уже работает несколько
десятков систем, но кризисные явления в пивном производстве задерживают широ-
кое распространение долгожданного технического решения. Для фильтрации сидра тангенциаль-
ные фильтры используются уже давно. Фильтрация кваса также не составляет проблем. Очень широко используются тангенциальные фильтры в производстве соков и их концентратов. Главным преимуществом тангенциальных фильтров является стабильно высокое качество фильтрации, полная автоматизация, компактность, минимум отходов. Основной недостаток этих фильтров – высокая цена снижает свою значимость с ростом цен на кизельгур и его утилизацию и появлением новых мембран с высоким ресурсом. Очень широко применяется в производстве напитков фильтрационный картон и изготовленные из него модули. Картон позволяет эффективно решать
фильтрационные задачи в очень широком диапазоне: от осветления до удаления микроорганизмов и коллоидов. Наиболее распространено использование картона в виде листов вследствие их дешевизны. Недостатки технологии листового картона (громоздкость и негерметичность фильтр- прессов, трудоемкость обслуживания) успешно устраняются применением модульных фильтров из картона. Все перечисленные методы исполь-
зуются на стадии производства или подготовки напитков к розливу. Но по пути готового напитка в тару он может быть повторно загрязнен частицами или микроорганизмами. Поэтому как можно ближе к розливу устанавливаются контрольные фильтры. Они могут быть механическими
или микробиологическими, соответственно. Основное требование к этим фильтрам – исключительная надежность, что означает гарантированное удержание накопленных загрязнений и устойчивость самой фильтрационной среды в условиях высоких динамических нагрузок на розливе. Микробиологические фильтры, кроме того, должны эффективно стерилизоваться (лучше термически) и тестироваться на целостность. Наибольшее количество проблем на этой стадии связано с использованием микробиологических фильтров. Перечисленным выше требованиям к микробиологическим контрольным фильтрам отвечают картриджные мембранные фильтры . Для разных напитков применяются фильтры с рейтингом 0,65, 0,45 или 0,2 мкм с одинарной или двойной мембраной из нейлона, полиэфирсульфона или тефлона. При грамотном подходе к инжинирингу систем микробиологической фильтрации результаты получаются безукоризненными.
Наиболее частыми ошибками здесь являются неправильная увязка фильтросистемы в инфраструктуру розлива, некачественные CIP-растворы, неэффективная стерилизация самих фильтров и связанных с ними продуктопроводов и арматуры. Результаты некачественного инжиниринга проявляются очень быстро – безвозвратно забитые дорогостоящие фильтроэлементы, испорчен качественный продукт и его репутация на рынке. Самым простым применением может показаться контрольная фильтрация водки. Но и здесь есть know how. Чем
меньше размер контрольного фильтра, тем меньшее влияние окажет свежий фильтр на продукт, и меньше сможет уместить загрязнений, которым незачем долго контактировать с высококачественным напитком. Очистка ополаскивающей воды для тары и оборудования, СО2 для карбонизации напитков, воздуха для емкостей – все это примеры применения фильтров для
вспомогательных сред. Наиболее часто требуются стерильные газ и вода, хотя можно удалять влагу и запахи из газов, частицы из пара, газов и воды. Все эти задачи эффективно решаются при помощи картриджных фильтров, но их решение никогда не ограничивается лишь установкой собственно фильтра. Для каждого конкретного фильтра разрабатывается схема его увязки в техно-
логическую схему и соответствующий регламент обслуживания, обеспечивающий надежность получения вспомогательной среды требуемого качества. Для стерилизующей фильтрации воды и газов используются фильтры с рейтингом задерживания 0,2 мкм, для удаления влаги из газа – фильтры- коалесцеры, для фильтрации пара – фильтры из пористой нержавеющей стали.
Фильтры для стерилизации газов должны быть мембранными, лучше с двойной мембраной, с хорошей пропускной способностью и гарантированным ресурсом стерилизаций паром. Они должны тестироваться на целостность. Газовые фильтры должны быть гидрофобными, иначе фильтр пропитается влагой и станет проницаем для микроорганизмов. При установке дыхательных фильтров на емкости необходимо обязательно устанавливать защитные устройства от высокого давления или низкого вакуума на случай блокировки фильтров.
Надеемся, что вышеприведенный обзор и рекомендации помогут правильно подойти к принятию фильтрационных решений. По вопросам, касающимся поставок фильтрационного оборудования и расходных материалов, конструирования, монтажа, оптимизации и сервиса фильтросистем предлагаем обращаться в ООО «Интер Технолоджи Компани» – официальному дистрибьютору в Украине фильтрационной корпорации Pall (США).